BaSys Industry 4.0 - An Open Platform for the Fourth Industrial Revolution
Today, manufacturing systems are designed for mass production of identical goods. Although manufacturing systems often have a certain flexibility, they are not completely changeable. Instead, changes are associated with high costs. Changeable production, on the other hand, allows manufacturers to respond more quickly to changing demand and to produce small batches efficiently.
In the BaSys4.0 project, the open-source middleware Eclipse BaSyx was constructed to allow a reference implementation of the concepts of Industrie 4.0. These concepts and implementations were taken up in the follow-up projects BaSys 4.2, BaSys4Transfer and the BaSysSatellite projects and are continuously developed and validated.
Challenges encountered in the engineering of fluid power systems
Fluid power drives are important "muscles" of a flexible Industrie 4.0-compliant production. The variety of possible circuits with different components and their extremely heterogeneous properties significantly influence engineering decisions in all phases of the product life cycle of a machine. To meet the challenges, the approach of an integrated model-based engineering process is being pursued. This makes it possible to test different scenarios and variants quickly and efficiently with simulation models in order to take decisions and make adjustments for the real machines. Thereby, the OEM has to consider in particular the specific properties of the fluid technology components, of which the know-how, data and parameters as well as detailed simulation models are, however, usually only available at the component suppliers.
The following challenges must be overcome for an integrated simulation-based development process:
- Cross-stakeholder availability of simulation models and the required parameters of real components for efficient and error-free configuration of a system simulation
- High availability of data and parameters and seamless linking across all development phases, e.g. during the transition from engineering to commissioning
- Linking of simulation models with the components installed in the machine and their state variables.
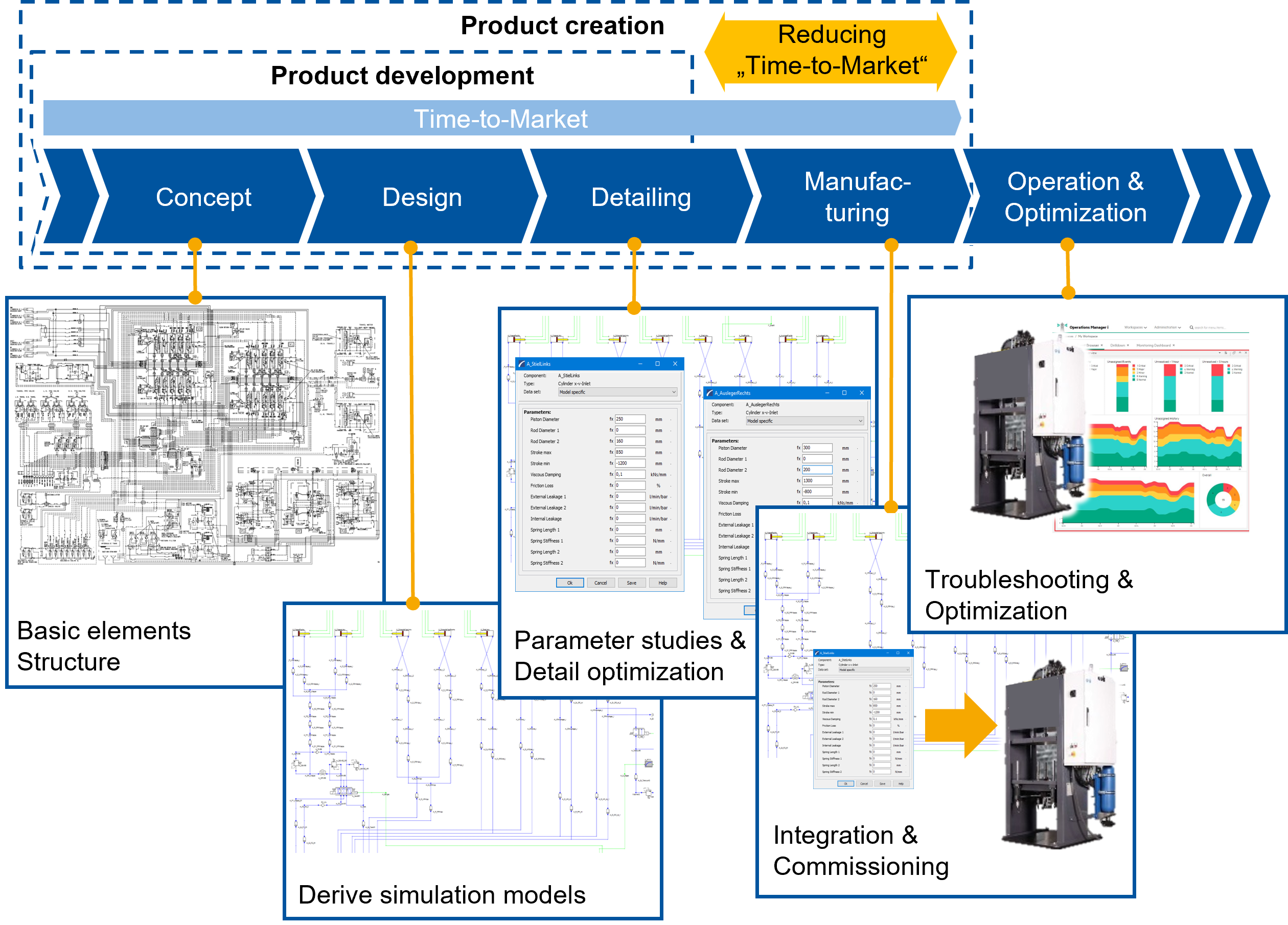
BaSys4FluidSim - Simulation framework of fluid power components for integrated and seamless engineering
The aim of the project is the development of a Industrie 4.0-capable simulation framework for an integrated and seamless simulation model-based engineering with the focus on:
- Domain-independent system simulation with a high level of detail across all integration levels
- Interoperability for cross-stakeholder use of simulation models while protecting specific know-how
- Cross-stakeholder availability of data for or from simulation models throughout the product lifecycle
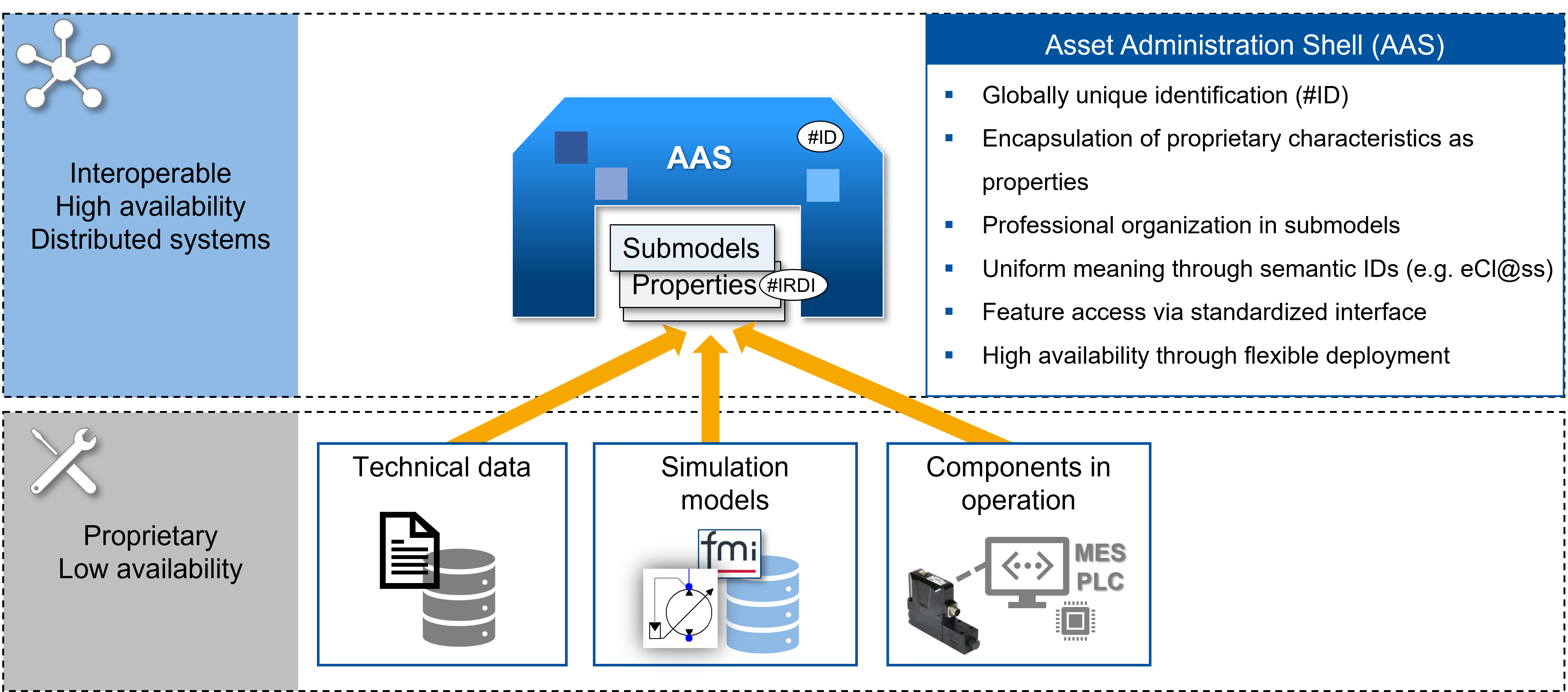
The key element for an Industrie 4.0-compliant implementation of the concept is the Asset Administration Shell (AAS). AASs are digital representations of the assets under consideration, such as a hydraulic component. They have semantically uniquely defined properties that represent information and services of the asset and make them available in encapsulated form. The characteristics of an asset relate to its use in a defined context at various stages of the product lifecycle and are then grouped and standardized accordingly in submodels. The uniform data model, the standardized semantics of the described characteristics, and a standardized communication interface improve the interoperability, availability, and integration capability of the assets under consideration.
With these properties, the AAS is the ideal basis for lifecycle and manufacturer-spanning value added networks in which all stakeholders can benefit. An implementation of such a life-cycle and manufacturer-spanning value network is carried out on the basis of three exemplarily selected use cases of simulation model-based engineering using the BaSys4FluidSim framework and the web-based simulation environment Fluidon | Cube.
BaSys4FluidSim - Use-Cases of simulation model based engineering
The first functionality of the framework (a) allows for searching and finding components or component simulation models. Their digital representations are located in repositories in the form of AAS, where they can be queried according to defined requirements of the desired application. Thus, in the context of simulation-based product development, the OEM can look for required component data and simulation models for its machines in the repositories of its component suppliers.
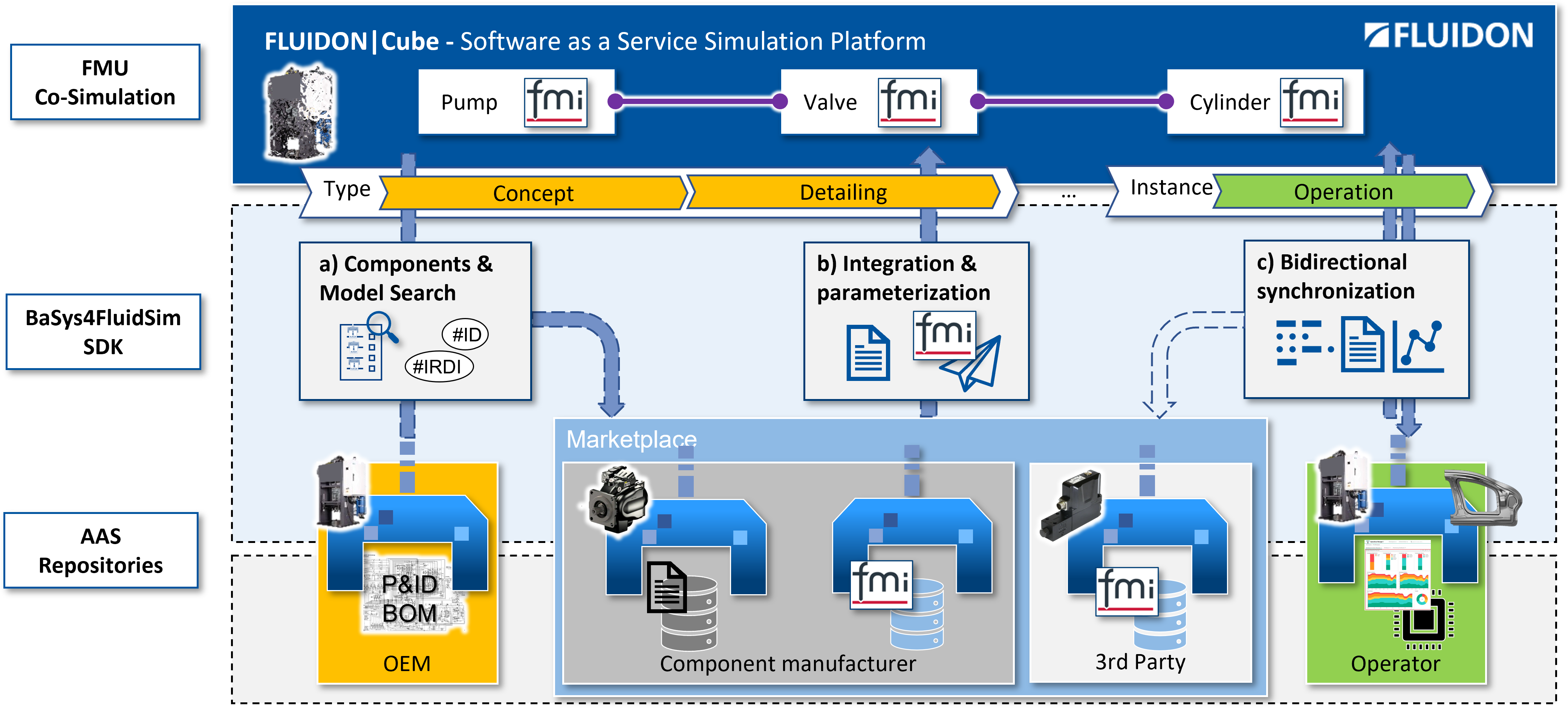
The second functionality (b) enables a domain and tool independent integration of component simulation models into a simulation environment. On the one hand, this integration is enabled by an automatic parameterization of simulation models with the available parameters from the AASs. The automatic parameterization reduces the time required and the error-proneness compared to the manual parameterization from a wide variety of parameter sources.Another option is the integration of a complete component simulation model as a Functional Mock-up Unit (FMU). FMUs are based on the Functional Mock-up Interface (FMI) standard and serve to encapsulate simulation models, in the case of co-simulation even including the appropriate integrator. Thus, the FMU-based approach supports a flexible, domain- and tool-independent deployment and, at the same time, protects the model creator's know-how through model encapsulation.
The third functionality (c) enables bidirectional synchronization of parameters and states between the simulation and the real components of a machine on the shop floor based on their AAS instances. This enables error investigation and correction on the real machine with the help of the simulation model or supports commissioning by allowing parameters already determined in the simulation to be transferred directly to the machine programmable logic control. In both cases, the transparency and thus the quality of the decisions to be made is increased for the specialist personnel with a significantly reduced expenditure of time.
Reference application of the BaSys4FluidSim project consortium
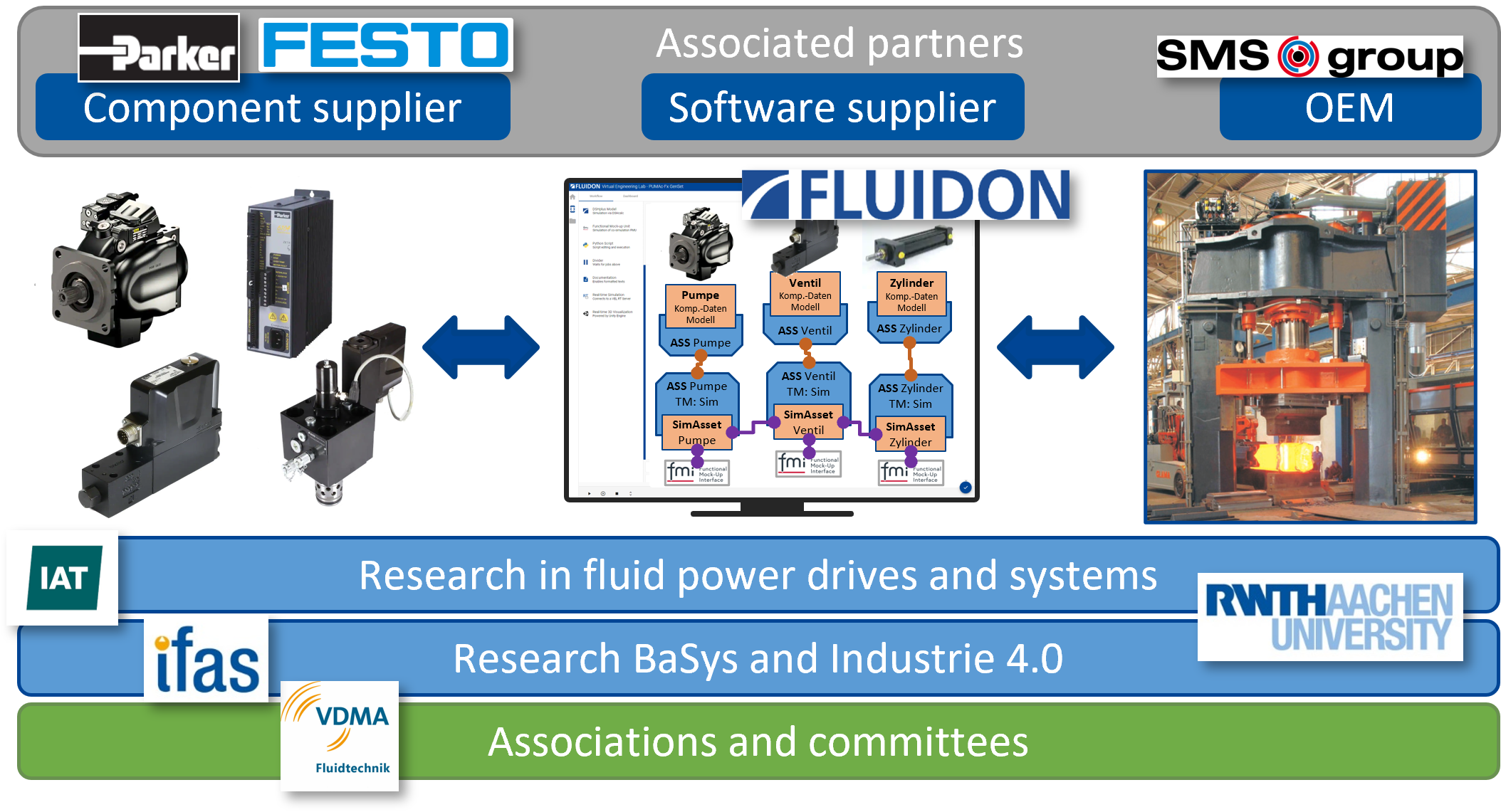
The objectives of the project will be validated using the example of a servo-hydraulic press from Parker (associated partner). By the implementation of all relevant aspects in the context of AAS and their validation on the practical demonstrator, a blueprint for future applications in industry is established.
Further information:
- 2023: Concept of a Simulation Framework for Seamless and Interoperable Linking of Components and Simulation Models for Fluid Power Systems, M. Becker, S. Heppner, R. Alt, T. Kleinert, K. Schmitz, DSEC Conference 2023