ESEMO - Development of Self-Monitoring Energy-Optimised Assembly Systems
The importance of energy is increasing in all sectors of the economy. Steadily rising energy costs and numerous governmental incentive measures are evidence of this trend. The area of industrial goods production is particularly affected by this, as rising energy prices lead to a significant increase in the cost share of the total production costs of industrially manufactured products.
Energy consumption is thus becoming an important influencing factor for the identification of optimisation potentials, because the issue of energy efficiency will gain increasing importance in pending purchasing decisions regarding new machines and plants.
The ESEMO project demonstrates the high potential of optimising process control with regard to more energy-efficient operation using the example of a self-piercing riveting machine. The project participants were ITQ GmbH, the Institut für Systemdynamik und Mechatronik (ISyM) at Bielefeld University of Applied Sciences, FLUIDON GmbH and Böllhoff GmbH & Co. KG.
Motivation
An important sector of industrial goods production is made up of machines and components of assembly technology, whose energetic aspects are currently only considered in a rudimentary way.
A major hurdle to the necessary systematic consideration of energy efficiency lies in the high system complexity of modern machines and plants, with their large number of parallel and sequential energy fluxes that influence each other.
It is not possible to evaluate the energy efficiency of a developed solution by means of simple system considerations. Due to the usually very small quantities - these often range from individual production to a few hundred machines - the time and financial expenditure of a systematic consideration of energy efficiency, allocated to a machine or system, is also very high.
Solution
The operating strategies and sequences implemented are essential for the energy efficiency of assembly systems. This area is almost exclusively covered by controller software. Consequently, an economically efficient methodology for determining and optimising the operating strategies from an energetic point of view is the logical solution approach.
However, this requires a detailed virtual behavioural model (digital twin) of the real machine or plant. In the ESEMO project, the control parameters of the RIVSET-Gen2r punch riveting system were optimised with the help of a digital twin created in DSHplus, thus reducing the energy consumption by a significant amount.
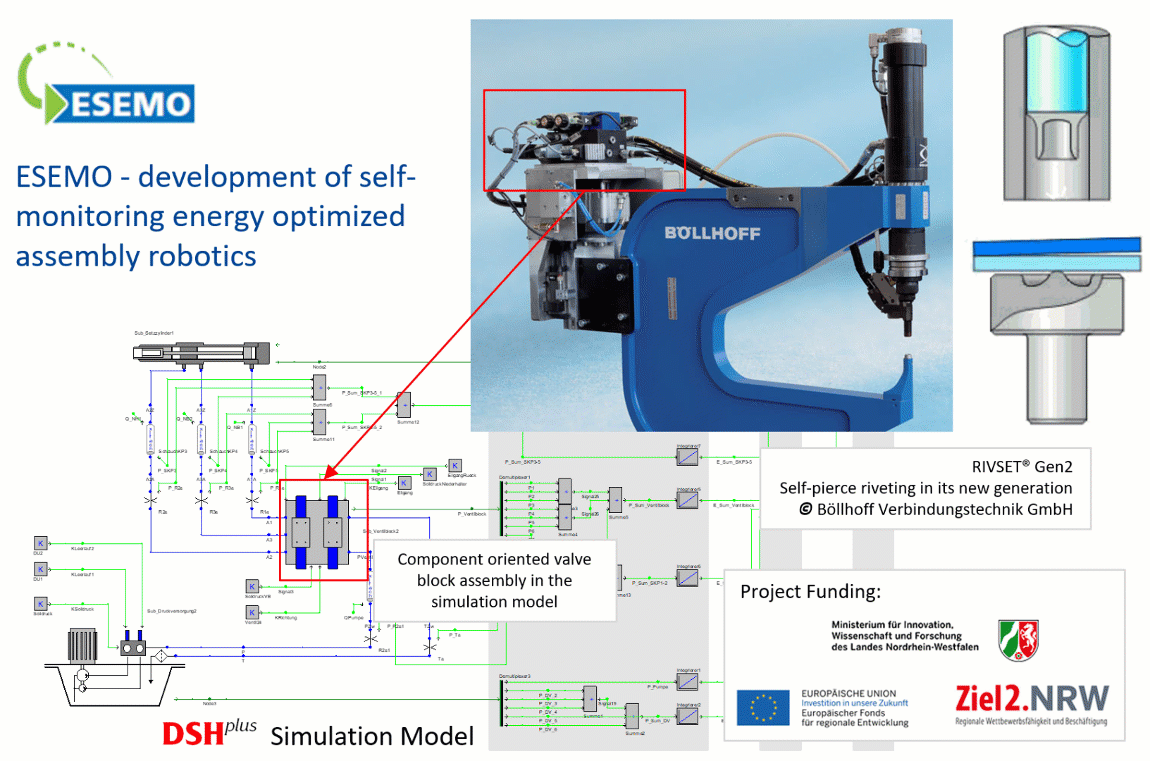