DSHplus Libraries: Intuitive and powerful component collections
Library overview
Hydraulic Library
The hydraulic library includes all standard components for the design of a hydraulic system and is oriented to the ISO 1219-1 standard to make models easy to understand.
Key features:
- Over 180 parameterizable models
- Structured subgroups such as pumps, valves and accumulators
- Physical models for detailed analyses
- Flexible expandability through user-defined components
Pneumatic Library
This library was developed in collaboration with the IFAS at RWTH Aachen and offers a wide range of functions for pneumatic systems.
Fields of application:
- Automation technology
- Chassis technology (e.g. air suspension and brakes)
- Mechatronic systems in the packaging industry
Additional function: Can be combined with DSHplus-STC and multi-body simulation for detailed analyses of air suspension in vehicles and machines.
Mechanics Library
The mechanics library allows you to construct oscillatory mechanical structures and analyze mechanical movements.
Functions:
- Simulation of one-dimensional mechanical systems
- Combination of translation and pivoting motion
- Investigation of positioning accuracy and angular errors
Control Library
This library offers a variety of block elements for developing control loops and controllers for a wide range of mechatronic applications.
Highlights:
- Signal sources, characteristic diagrams and mathematical functions
- Time-discrete and analog transmission elements
- Non-linear switches and limiters
- Equation interpreter for processing mathematical formulas (muparser)
- User-definable function blocks
Particle and Filtration Simulation
This function supports the analysis and optimization of filter concepts in hydraulic systems.
Benefits:
- Simulation of particle distribution in the hydraulic line system
- Evaluation of filter performance
- Planning of maintenance cycles to reduce downtime
Customized Libraries
FLUIDON offers the development of component libraries that are precisely tailored to customer requirements.
Typical applications:
- Internal development projects
- Support of customer acquisition by providing ready-to-use libraries
Library for Handling Fluid Properties
This library provides tools for managing and simulating fluid property data.
Key topics:
- Equation- and table-based fluid descriptions
- Representation of vapor pressure curves and gas dissolution properties
- Simulation of vapor and gas bubbles in piping systems
Fluid Handling in DSHplus
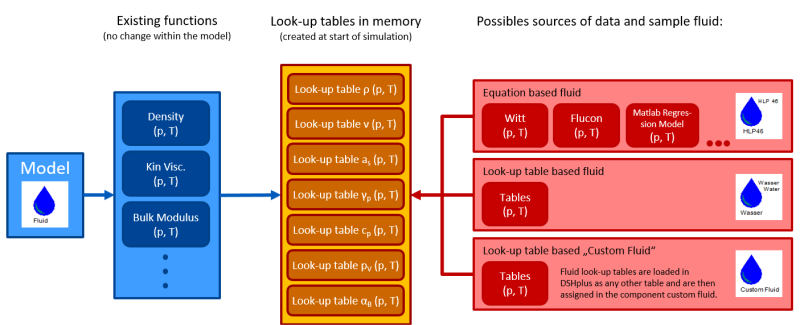
Why DSHplus?
With DSHplus and its libraries, engineers can efficiently model, analyze and optimize complex fluid power systems. The software covers all the essential requirements and offers an intuitive structure that delivers precise results and makes work easier for engineers.
Contact us now to learn more about DSHplus and how it can be used in your company.