Real-Time Simulation With Cube-RT
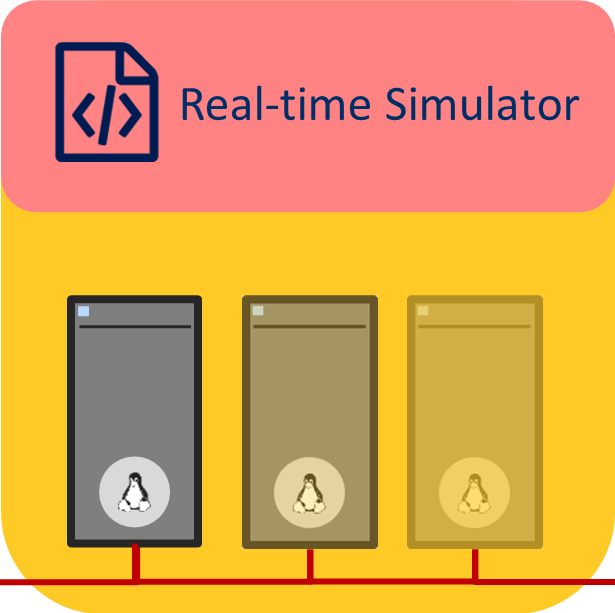
The Cube Real-time Simulator is the calculation framework for real-time capable digital twins of Fluidon Cube - The Virtual Engineering Lab. The Real-time Simulator is based on a real-time capable Linux system that is suitable for both hard and soft real-time requirements in automation technology.
The Real-time Simulator requires digital twins (simulation models) that are created as FMUs according to the "FMI Co-Simulation (Stand Alone) 2.0" standard for Linux 64bit. To connect the digital twins to the real world, the Real-time Simulator has an EtherCAT master that uses the EtherCAT protocol described in IEC standard 61158.
The Real-time Simulator runs on standard PC hardware, to which FLUIDON merely adds an EtherCAT-capable network card.
In the course of an engineering project, FLUIDON procures the PC hardware for the customer, configures the Real-time Simulator for him and creates the digital twin. Following introductory training, the customer is able to use Fluidon Cube for independent development work after the project is concluded.
Requirements for Real-Time Simulation of Fluid Power Systems
Real-Time-Computing (RTC) describes hardware and software systems that are subject to a "real-time constraint", e.g. from event to system response. Digital twins having real-time requirements must meet this constraint and guarantee a reaction within certain time specifications. Digital twins for fluid engineering systems however are subject to some special, domain-specific requirements.
- For physically modelled fluid engineering systems, where e.g. the inductance of the pipeline is also to be taken into account, the simulation step sizes are typically in the range of 1e-5 to 1e-6 s. As the simulation model size increases, it becomes increasingly difficult to solve all the associated equations in real time as well. Many out-of-the-box simulation tools, unable to guarantee the real-time capability of their simulation models in every case, have to simplify the model dynamics at this point to meet the real-time requirement.
- As an engineering service provider and supplier of simulation tools FLUIDON use its experience to develop your customer-specific or problem-specific solutions with regard to the real-time capability of the fluid engineering simulation model and its synchronisation.
- With "split, cut and parallelize" not only a parallelisation of the involved domains is carried out, but the models are subdivided into smaller subsystems until the computing time of the overall model corresponds to the real-time requirement. FLUIDON has gained the necessary experience for efficient model partitioning in more than 20 years of practical applications in the field of co-simulation of fluid power systems and through collaboration in numerous research projects.
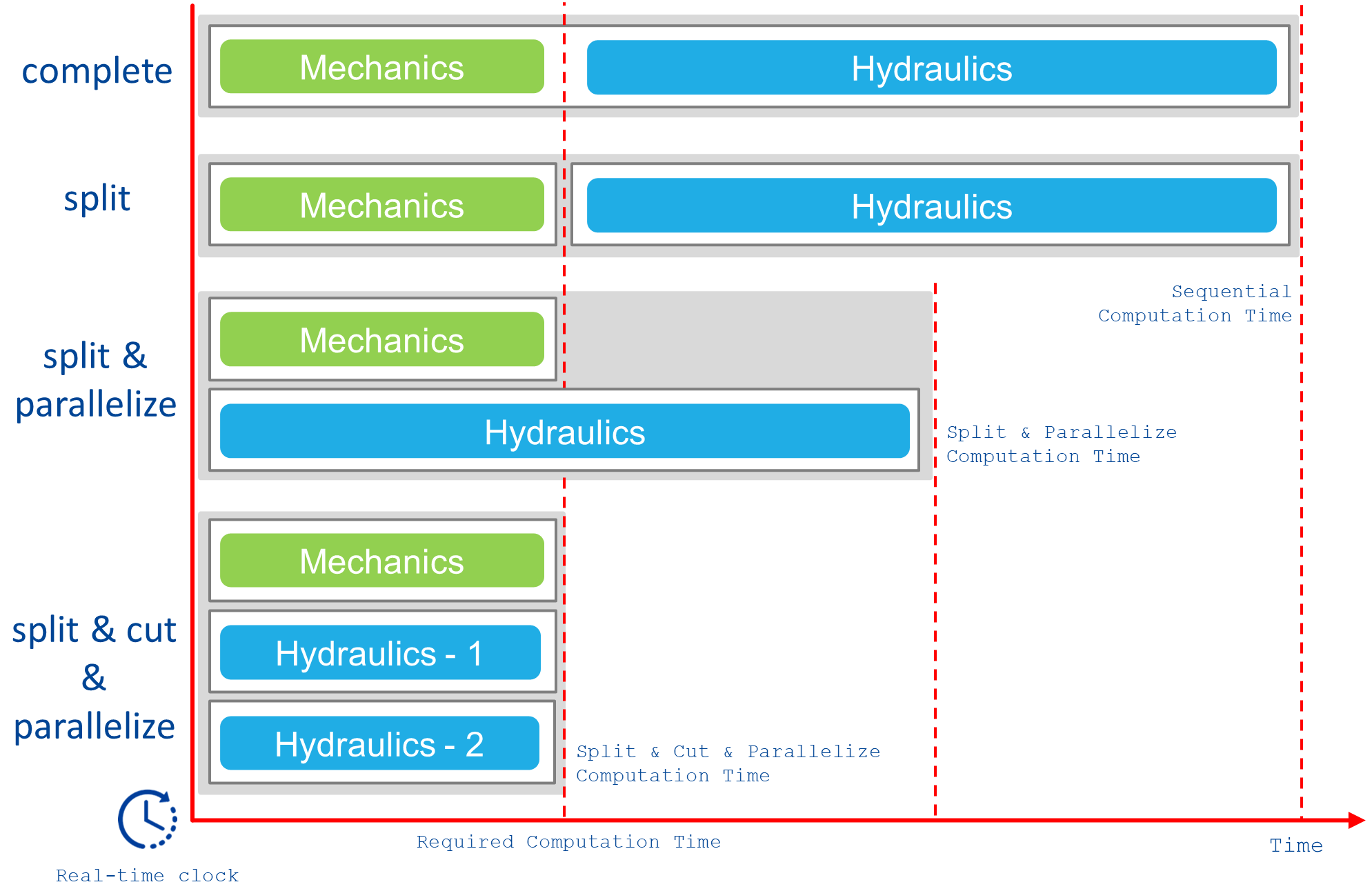
Working With the Real-Time Simulator
- The Real-time Simulator is able to manage several digital twins in parallel. An I/O mapper takes over the linking of the digital twins.
- Depending on the required computing power, the digital twins can be calculated on a high-performance multi-core computer or, if the numerical stability of the network permits, distributed over several computers connected to the EtherCAT network.
- In both cases, the Real-time Simulator synchronises the calculation of the digital twin(s) with the real-time clock of the framework and exchanges input and output signals with the HiL setup of Fluidon Cube according to the user-defined assignment.
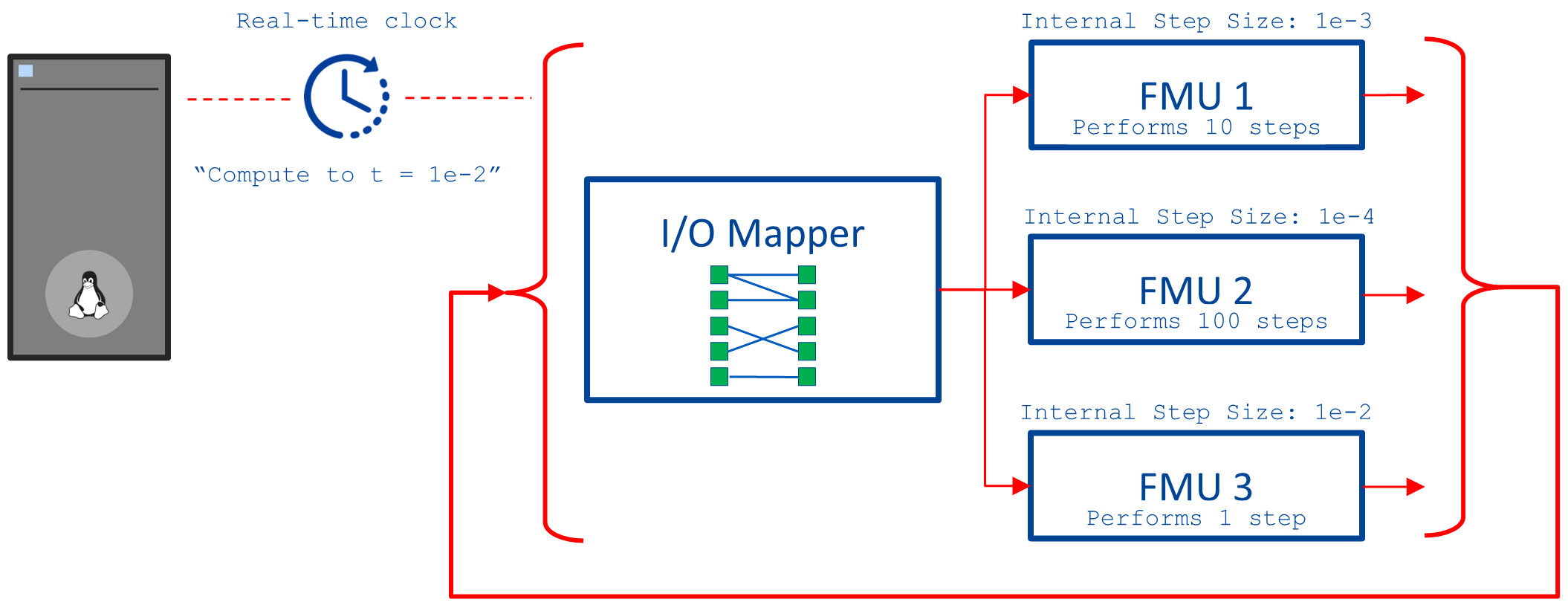