Virtuelle Inbetriebnahme
Die virtuelle Inbetriebnahme stellt einen Teil oder Ausgangspunkt eines zukünftigen Produktlebenszyklusmanagements dar, das vollständig durch die Digital-Twin-Methodik unterstützt wird.
“The digital twin is disrupting the entire Product Lifecycle Management (PLM), from manufacturing to service and operations. Nowadays, PLM is very time consuming in terms of efficiency, manufacturing, intelligence, service phases and sustainability in product design. A digital twin can merge the product physical and virtual space. The digital twin enables companies to have a digital footprint of all of their products, from design to development and throughout the entire product life cycle.” (Zitat aus Wikipedia)
Vorteile im Überblick
- Gewinn an Zeit
- Unterstützt interdisziplinäres Arbeiten
- Führt zu einer detaillierte internen Produktdokumentation
- Generiert eine umfangreiche interne Wissensbasis
- Ermöglicht Softwareentwicklung und -tests in der Software-in-the-Loop (SIL)-Umgebung
- Validierung kann auf realer SPS in der Hardware-in-the-Loop-Umgebung (HIL) erfolgen
- Erlaubt Anwender- oder Kundentests und Feedback auf Basis des virtuellen Prototyps
- Zeigt Designprobleme viel früher auf
- Ermöglicht kostengünstigere Korrekturmaßnahmen
- Führt zu einer besseren Qualität des Produktdesigns
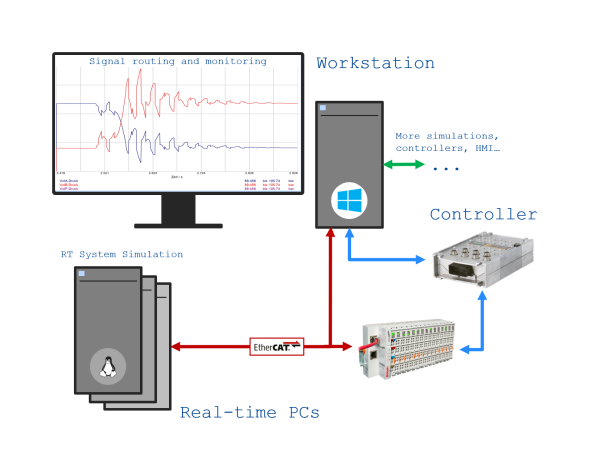
Vorteile der Virtuellen Inbetriebnahme im Detail
Die virtuelle Inbetriebnahme basiert auf dem digitalen Zwilling eines technischen Systems oder Subsystems, das die verschiedenen relevanten technischen Bereiche wie Mechanik, Hydraulik, Elektronik und Software vereint. Doch betrachten wir zunächst das "Warum". Was sind die Ziele und Vorteile der virtuellen Inbetriebnahme?
Einer der wichtigsten und offensichtlichsten Vorteile ist der Zeitgewinn im Vergleich zum klassischen Prozess, der in der folgenden Abbildung visualisiert wird:
Ein großer Teil der Integrations- und Inbetriebnahmearbeiten kann bereits durchgeführt werden, bevor ein realer Prototyp der Maschine existiert.
Die Vorteile der virtuellen Inbetriebnahme gehen jedoch weit über diesen Aspekt hinaus. Wie die obige Abbildung auch zeigt, trägt jede Ingenieursdisziplin, wie Mechanik, Elektrotechnik und Softwaretechnik, zum digitalen Zwilling bei, so dass interdisziplinäres Arbeiten und Kommunikation in einem frühen Stadium der Produktentwicklung gefördert werden. Der resultierende digitale Zwilling stellt eine hervorragende interne Produktdokumentation und Wissensbasis dar.
Die virtuelle Inbetriebnahme bietet insbesondere für die Elektronik- und Softwareingenieure einen großen Nutzen: Während im klassischen Prozess die Softwareentwicklung und der Test oft nur am realen Prototypen erfolgen kann, erfolgen nun die Softwareentwicklung und -tests in der Software-in-the-Loop (SIL)-Umgebung mit dem virtuellen Prototypen. Nach Auswahl der geeigneten Hardware finden die weitere Validierung auf der realen SPS in der Hardware-in-the-Loop-Umgebung (HIL) statt. Die Mensch-Maschine-Schnittstelle (MMS, engl. Human-Machine-Interface HMI), bestehend aus Komponenten wie Joysticks, Bedienfeldern und Displays, kann bereits Teil dieses Testaufbaus sein und ermöglicht nicht nur einen Test aus Engineering-Sicht, sondern auch Anwender- oder Kundentests und Feedback auf Basis des virtuellen Prototyps. Extremsituationen der Maschine können in dieser Phase ohne Risiko getestet werden.
Diese frühe Integration deckt Designprobleme viel früher auf als der traditionelle Prozess, ermöglicht somit kostengünstigere Korrekturmaßnahmen als in einem späteren Stadium und führt zu einer besseren Qualität des Produktdesigns.
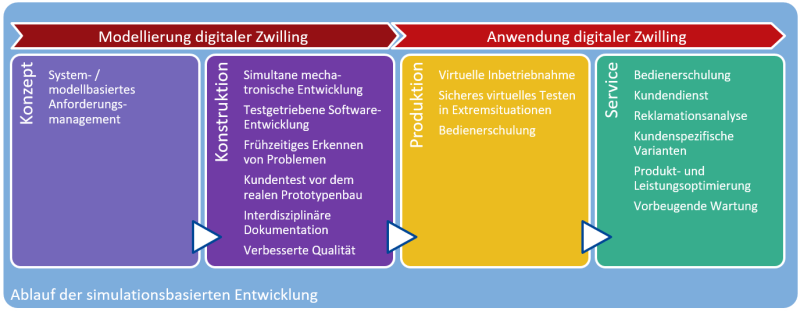
Virtueller Prototypenbau - Die ersten Schritte zum digitalen Zwilling
Der virtuelle Prototyp bildet den Kern der virtuellen Inbetriebnahme. Der Aufbau und die Verfeinerung dieses Prototyps sind ein wesentlicher Bestandteil der Konstruktionsarbeit. Auch wenn jede Ingenieursdisziplin "ihr" Modell aufbaut, erfordert es interdisziplinäre Arbeit, um die Schnittstellen zwischen den verschiedenen Teilmodellen zu definieren und einzurichten. Designprobleme aufgrund fehlender Kommunikation werden so minimiert. Dieser Prozess zwingt zudem dazu, alle Komponenten auf einem adäquaten Niveau zu spezifizieren und zu dokumentieren, wodurch die Qualität der Konstruktionsdokumentation verbessert wird. Die Auswirkungen von Konstruktionsänderungen werden für das gesamte Konstruktionsteam sichtbar.
Der folgende Workflow ist ein Beispiel für die virtuelle Inbetriebnahme. Die dargestelten Arbeitsschritte werden parallel ausgeführt, typischerweise in mehreren Schleifen, beginnend mit der "groben" Modellierung bis hin zu einer verfeinerten virtuellen Darstellung der Maschine mit ausreichender Genauigkeit.
Erstellung eines mechanischen Modells des relevanten Maschinen-Subsystems
Auf Basis von
- 3D-CAD-Daten
- Werkstoffdaten
- Daten der Komponenten
wird ein kinematisches Modell der Maschine und / oder des Subsystems erstellt.
Die Schnittstellen zu den "benachbarten" Domänen, z.B. zur Hydraulik, werden beim Modellaufbau entsprechend berücksichtigt.
Nach dem erfolgreichen Modelltest wird das Mechanikmodell als FMU exportiert und steht für die Kopplung mit FMUs aus weiteren Domänen zur Verfügung.
Erstellung eines Hydraulikmodells
Eine ähnliche Vorgehensweise, wie bei der Modellierung der Mechanik, erfolgt bei der Hydraulik. Informationen für die Modellerstellung der Hydraulik können aus
- Schaltplänen
- Stücklisten
- Komponentendaten von Zulieferern
(z.B. Beschreibung des dynmaischen Ventilverhaltens)
entnommen werden.
Auch das Hydraulikmodell wird nach Fertigstellung als FMU exportiert.
Verbinden der einzelnen FMUs zum Digitalen Zwilling
Nachdem die einzelnen, domänenspezifischen Modelle erstellt und als FMU exportiert worden sind, können sie nun zum Digitalen Zwilling der Maschine oder des relevanten Maschinen-Subsystems zusammengefasst werden.
Dabei müssen die Teilmodelle lediglich an den zuvor definierten Schnittstellen verbunden werden.
Das Ergebnis ist die sogenannte Composite FMU.
Realtime-Simulation des Digitalen Zwillings
Erstellung der Applikationssoftware
Visualisierung des Maschinen- / Subsystemverhaltens
Mit Hilfe der virtuellen Inbetriebnahme können die entwickelten Maschinenfunktionen überprüft werden. Dabei ist es hilfreich die relevanten Größen zu visualisieren.
Fluidon Cube bietet die Möglichkeit zur Visualisierung von Prozessdaten in 2D, stellt das Bewegungsverhalten kompletter Maschinen aber auch in 3D dar.
Der Beispielworkflow für die virtuelle Inbetriebnahme zeigt, dass ein großer Teil der Arbeiten des klassischen Entwicklungsprozesses nun Teil des modellbasierten Arbeitens wird: Die Softwareentwicklung, -prüfung und -verbesserung bis hin zur Voreinstellung der meisten Parameter erfolgt während des virtuellen Prototypenbaus.