Welcome to FLUIDON - Pioneers in the simulation of fluid power mechatronic systems
FLUIDON stands for know-how in the field of fluid power. Our agile team of well-coordinated fluid power experts designs reliable, custom-fit and on-time solutions for our customers from across the globe.
Over 25 years of service experience in the analysis and optimisation of hydraulic and pneumatic systems for automotive, aerospace, railway, naval, mechanical engineering, plant construction, mobile hydraulics or health technology make FLUIDON a dependable engineering partner for the industry. Our striving for innovation and the gained expertise manifest themselves in the continuous improvement of tried-and-tested engineering tools and the development of new ones.
Our in-house simulation environment DSHplus serves as a powerful tool for the dynamic, non-linear calculation of complex, combined fluid power and mechatronic systems. It is also of great value for concept analysis, system revision, component selection and design, fault diagnosis, function validation and training purposes.
The use of our Fluidon Cube - the Virtual Engineering Lab, an expandable development environment for building and orchestrating simulation models, allows unlocking the full potential of the “digital twin” concept. The VEL makes virtual commissioning available at low cost and is fit for the world of "Industrial Internet of Things".
FLUIDON offers its customers customised solutions through extensive fluid power expertise combined with needs-optimised simulation software and “Industry 4.0”-capable engineering tools.
It is FLUIDON's aspiration to be...
- the first point of contact for all those involved in the model-based development of fluid power systems
- a renowned consultant and solution provider for vibration problems in piping systems
- a provider of leading engineering tools for fluid power
- a reliable development partner for our customers' fluid power innovations
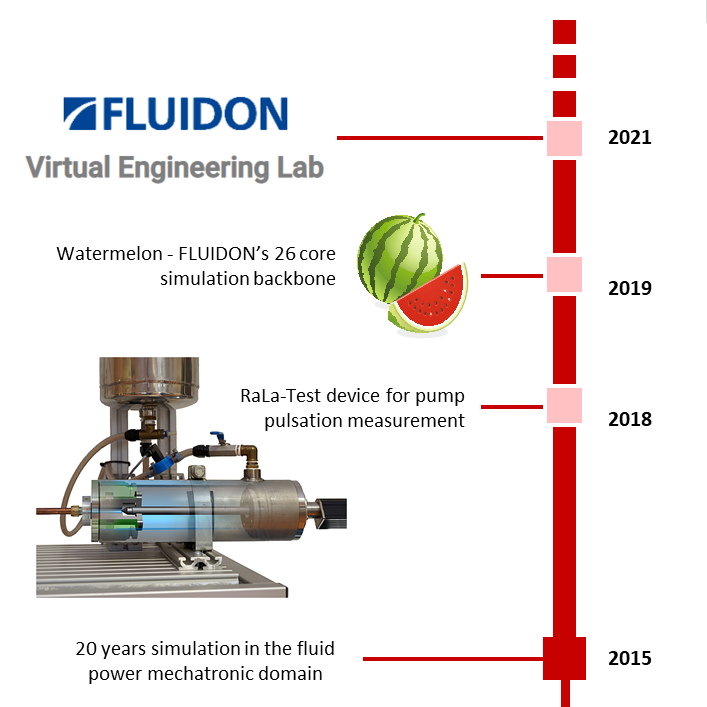
FLUIDON from 2014 to date
- Release of the Virtual Engineering Lab (VEL) als as a modular, extensible development environment based on open-source toolkits and standardised interface definitions for building and orchestrating simulation models.
- Virtual commissioning as an integral part of the offered services.
- Development of expert knowledge in the field of pressure oscillations in pipe systems.
- Extension of the DSHplus libraries in the areas of pipeline simulation, fluid-structure interaction, fluid properties and cavitation.
- Functional Mock-up Interface (FMI) standard replaces DSHplus STC.
- Test bench with low-reflection pipe termination (RaLa) for measuring pressure oscillations and pulsations generated by hydraulic displacement pumps and motors.
- OptiELF research project - optimising the energetic efficiency of hydraulic systems in vehicles.
- VeriSim research project - Development of measurement methods for the verification of a novel approach to simulate sound wave propagation in fluid power pipe systems.
- ESEMO research project - Development of self-monitoring energy-optimised assembly systems.
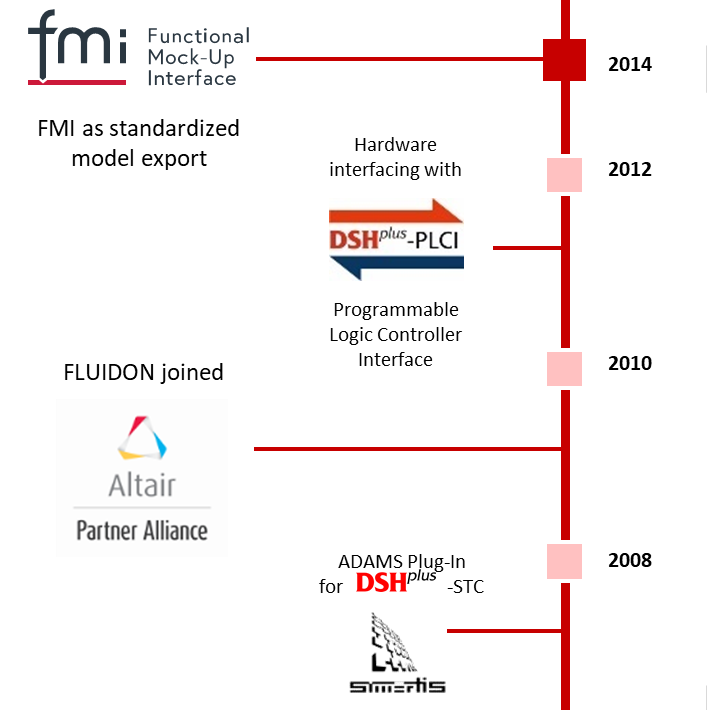
FLUIDON from 2007 to 2013
- The PLC interface closes the gap between system simulation and control development and lays the foundation for virtual commissioning. Designers and Developers can test the control of the machine without any risk before its commissioning and still benefit from realistic system behaviour.
- FLUIDON becomes a partner of Altair. This enables users to collaborate with tools from the HyperWorks platform via the Altair Partner Programme and provides access to the worldwide demand for development tools.
- The further development of DSHplus grants users access to the new libraries “particles and filters” as well as “mikro components”.
- FLUIDON invests in the expansion of a test bench laboratory for the measurement of customer components and validation of simulation results.
- GUSMA research project - Coupled, cross-company simulation of mobile machines for virtualisation of product development.
- KonZwi research project - Increasing the efficiency of a constant pressure system by means of an intermediate pressure pipe.
- Fluidtronic research project - Development environment for mixed fluid power and-mechatronic systems
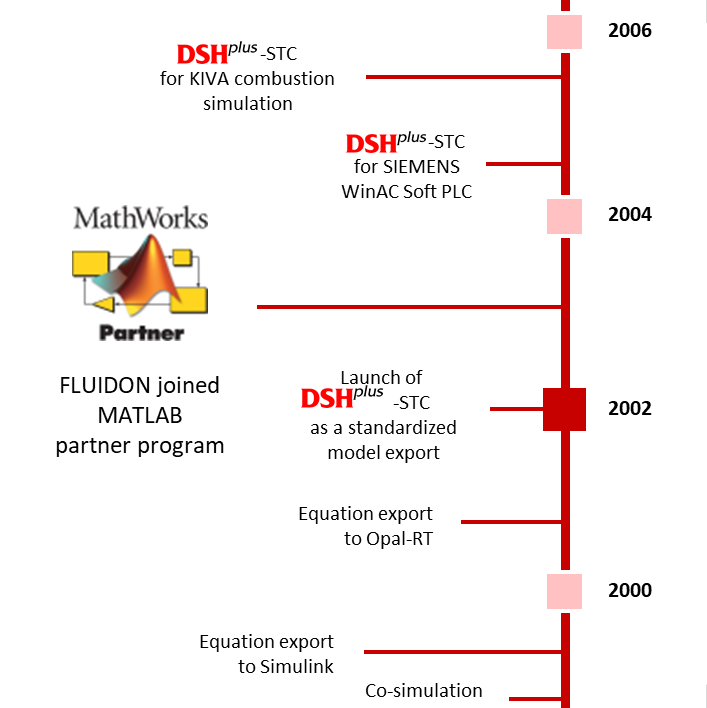
FLUIDON from 1999 to 2006
- Leading companies from a wide range of technical fields all over the world rely on DSHplus for the simulation of complex fluid power and mechatronic systems.
- In the systems to be simulated, dynamic effects like pressure oscillations or associated vibration problems are usually the focus of the computer-aided analyses.
- DSHplus offers libraries for hydraulics, pneumatics, mechanics, control engineering, a large number of tools for pre- and post-processing as well as modules for parameter variation, system optimisation or frequency analysis.
- DSHplus models are based on an open model source code, which gives the user a better understanding of the system and which can - of course - be locked when the models are passed on.
- The DSHplus Simulation Tool Chain (STC) enables diverse model export and import. In addition to the various interfaces to other tools (e.g. multi-body simulation software), a wide variety of hardware connections for hardware-in-the-loop simulation or coupled PLC simulation are available.
- User conferences guarantee a lively exchange with customers and users among each other.
- FLUIDON becomes a participant of the MATLAB partner programme.
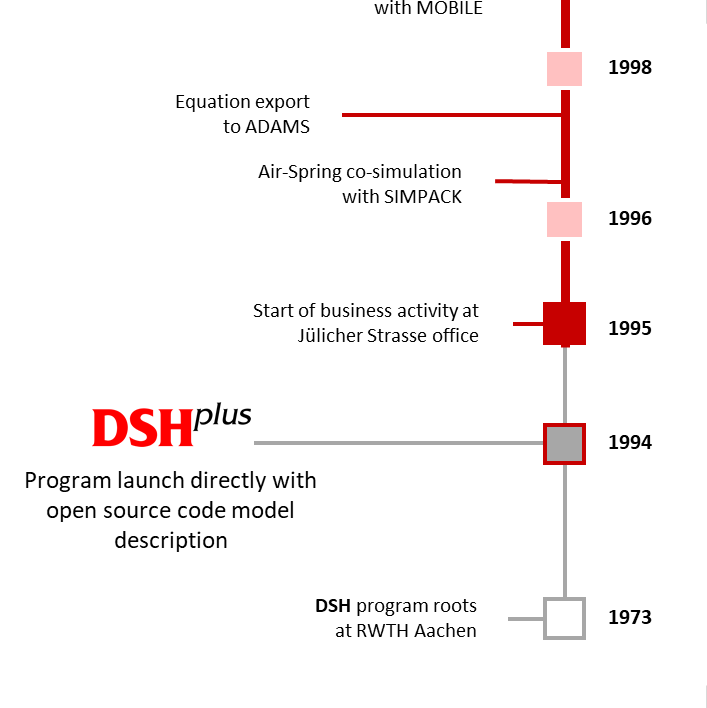
FLUIDON from 1973 to 1998
- As a spin-off of RWTH Aachen University, FLUIDON's DSHplus software profits from decades of experience gained at the internationally most respected chair in the field of fluid power, the Institute for Fluid Power Drives and Systems (ifas).
- The ongoing close cooperation with ifas enables a timely knowledge transfer and guarantees a continuous updating of our expert knowledge in the field of hydraulics and pneumatics.
- The beginnings of DSHplus date back to the 1970s, when numerical simulation was used for the first time to design hydraulic systems at the Institute for Hydraulics and Pneumatics (IHP) at RWTH Aachen University.
- Today's DSHplus program was developed at the Institute for Hydraulic and Pneumatic Drives and Controls (IHP) as a re-engineering of the DSH (Digital Simulation Hydraulics) and SIMULANT software packages.
- There is an interesting historical espionage incident about DSH from the times of the "Cold War"